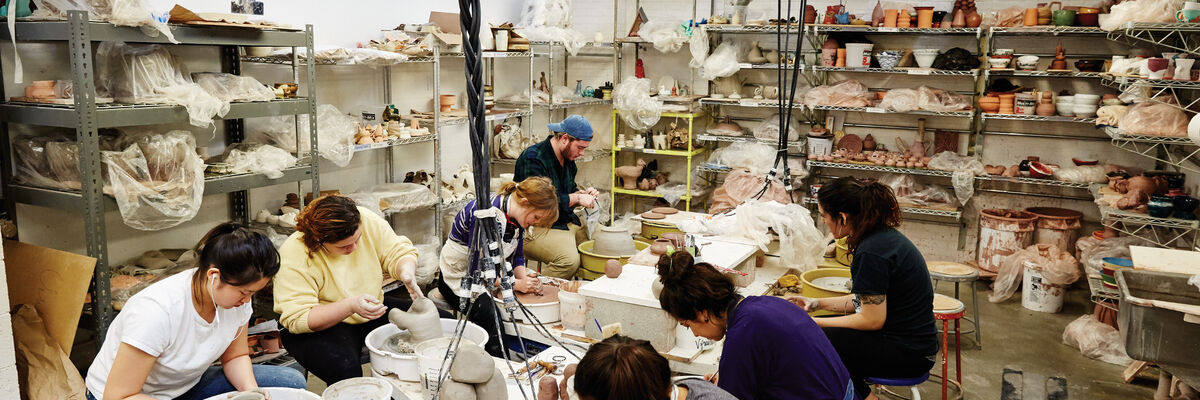
3D Printing: Rise of the 3D Machines
A blue light glows inside the black, cubed frame of the MakerBot Replicator 2. Its printer head crosses the x- and y-axes, depositing a layer of plastic along a circular path, in-filled with a honeycomb pattern. The platform drops a fraction of a millimeter on the z-axis, and another layer begins. The third dimension—height—is added.
The desktop 3D printer has a mysterious quality. The machine is carrying out an unseen set of instructions. Over the course of an hour, a 3D object begins to materialize on a previously empty platform.
"It's a very alchemical process, seeing these objects printed from nothing. It was very magical and bewitching, and I just felt that I had to incorporate it in my own work," says Tom Burtonwood, who uses 3D printing in two of the classes he teaches at SAIC. Burtonwood teaches Research Studio II: Adventures on Planet Xerox in the Contemporary Practices department as well as Hybrid Objects: Digital Sculpture in the Sculpture department.
Adventures on Planet Xerox takes science fiction as its jumping-off point. Students explore the ideas of copying, transmitting, and reassembling objects in three dimensions using examples from Star Trek: The Next Generation and the real-world technologies that bring those ideas closer to reality—such as MakerBot's Thingiverse, an open design community where people can share 3D files for objects under the creative commons license, and open source software and hardware.
Desktop 3D printing owes its existence to a community of developers committed to open source. Three-dimensional printing is not new. For nearly 30 years, large corporations have been using expensive 3D printers to prototype mass-produced products. In 2005 Adrian Bowyer, a British engineer and mathematician, founded the RepRap project. He was intensely interested in making an open source, inexpensive self-replicating machine and landed on the 3D printer as the ideal framework. Bowyer immediately publishes all of his work on his blog so that it is shared with the community and cannot be patented. With this technology, he intends to do nothing short of changing the world.
In a 2011 Kickstarter video by RepRap community members Relative Design, Bowyer says: "If RepRap takes off and increases its abilities by evolution to manufacture more and more products, then people having these machines in their homes will mean there will no longer be a need—or there will no longer be such a big need—for factories to make the things that they want.... And thus, we have short-circuited a large part of the conventional supply chain for material goods to individuals."
RepRap is moving closer and closer to being a fully self-replicating machine and remains completely open source. Anyone can download the files for free, print a large percentage of the machine's parts, buy the remaining few, and assemble it.
The self-replicating machine can be useful in remote areas of third-world countries where access to traditional supply chains is limited, Bowyer told the Guardian in July 2008. Also, if humans are to travel deep into space, we will need a way to manufacture new parts for broken machines without waiting for a shipment from Earth, according to Burtonwood.
In the hands of an artist, desktop 3D printers open up endless possibilities. "What makes 3D printing unique as a medium is the ability to quickly make objects that are very complex," says Burtonwood.
He bought his first 3D printer, a MakerBot Replicator 1, whose source code is based largely on the RepRap, in May 2012. He has created an accordion book titled Orihonin which each page is a 3D-scanned object from a museum collection, and this January he will be the Artist-in-Residence at the Art Institute of Chicago, scanning and printing objects from the museum's collection. He also has an exhibition running through February 22 at Firecat Projects in Chicago called Dialogues on the New Plastic.
Burtonwood notes that 3D printing allows for an iterative process not available through any other medium. The increasing affordability of the machines and materials allows artists to move through multiple iterations in a very short time without worrying about cost.
"When the cost of failure...is minimized, it encourages innovation. You're not thinking, ‘This is going to cost me a hundred dollars or two hundred dollars to make, and it might not be right,'" Burtonwood explains.
Brian Anderson, an instructor in SAIC's Department of Architecture, Interior Architecture, and Designed Objects, ran with the idea in his classroom last summer. He partnered with Printrbot to bring the company's (then $250) Printrbot Simple 3D printing machines into his course, Refresh: Summer Intensive, which culminated with a video exhibition of student work called Immediate Objects: Explorations in 3D Printing. Anderson equipped the classroom with one printer for each student, creating one of the first classroom experiences of this kind.
The course took place the summer before Master of Design (MDes) in Designed Objects students began their degree program. They worked with many of the school's resources, but focused intensively in their final weeks with the printers and made videos of their work.
The students printed with a popular plastic called polylactic acid (PLA) and nylon, a slower-printing and less forgiving material. To finish their nylon prints during class time and work with the slight misalignments that happened as they learned to use printers, they decided to print flat—two or three layers on average.
"It seems like a step back in what 3D printing can do, but in a sense, it's doing what 3D printing does really well: it takes a material and lays it down one layer at a time," Anderson says.
Some students ended up essentially printing nylon textiles, something Anderson plans to continue exploring in his own practice, and perhaps extend to a new class where he and the students build a printer large enough to print yardage.
Anderson first came to 3D printing himself as an MDes student at SAIC. The introduction was practical. He says, "I just needed to get a shape out that couldn't be made in any other way." Several years after his initial encounter, he decided to purchase a MendelMax 2.0 3D printer for his studio. This machine, he says, is more about speed than quality. The end product is not as polished as one from a MakerBot, but he can very quickly make substrates, or "bird bones," that can be skinned in more interesting, sculptural ways.
"I think it could bring 3D printing aesthetic to a more human and natural level because you can take these substrates and dip them in different material, and then you've got something that's regular, but also irregular," Anderson says.
Moving beyond the mass-produced quality of 3D printed objects is something that also interests Christian Oiticica, third-year Bachelor of Fine Arts student at SAIC. He completed Burtonwood's Adventures on Planet Xerox course and works in the Contemporary Practices digital resources lab, which houses three MakerBot Replicator 2s.
"A lot of my sculptures have little issues with them...that can't be replicated," Oiticica says. "So if overhangs fall apart, I'll let them fall apart because it gives uniqueness to the material."
This intimacy with the technology—making the artistic judgment to allow an object to fall as it is printing—is only made possible by desktop 3D printing. To use the industrial, $30,000 machines, a student fills out an order form and delivers it along with a digital file to the lab. Days or weeks later, the student picks up the model. "It's a black box," says Anderson.
A 3D printer, according to Anderson, is at its heart a Cartesian robot, meaning its principal axes of control are linear: x, y, and z. Laser cutters and computer numerical control (CNC) machines work on these axes as well.
He imagines his students gained an intuitive understanding of the technology this summer that they can carry with them through the degree program and their career. "Not only did they have a one-to-one relationship with these printers, but they had to get in there and make them work. And they had to view them as what they are...simply machines," he says.
Burtonwood notes that it is critical to introduce technologies like this right at the start of the educational experience so students can make informed choices about the work they do. Like Anderson, he sees 3D printing as both a technical skill for transforming ideas into objects as well as a wide-open frontier, ready to be explored and reinterpreted.